Guide to Robot Arm Enemy in Strider NES Version
By:Admin
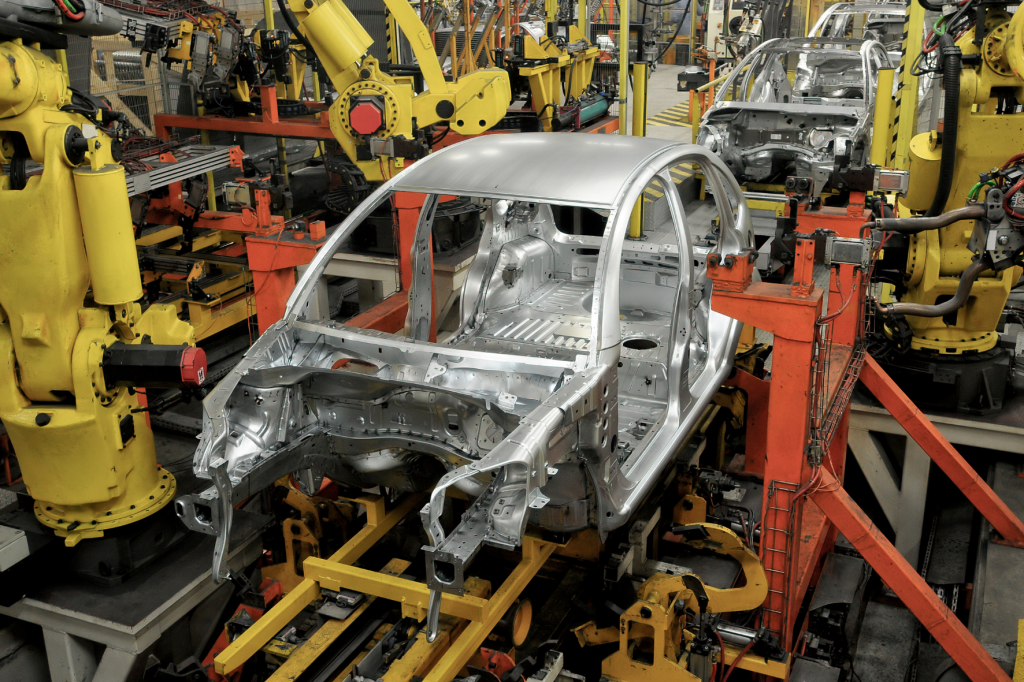
In today's fast-paced world, businesses are constantly looking for solutions that can increase efficiency and productivity while simultaneously reducing costs. One area that is gaining significant attention in this regard is industrial automation. And at the heart of this revolution is the Robot Arm Claw – a device that is transforming the way industries operate.
What exactly is a Robot Arm Claw?
A Robot Arm Claw is essentially a robotic arm with a claw or gripper at the end. It is programmed to perform a variety of tasks that enable efficient and autonomous operation of industrial machinery. The arm's movements are controlled by a computer that is pre-programmed to carry out specific tasks, such as pick-and-place operations, assembly, and sorting.
Benefits of Robot Arm Claws
Robot Arm Claws offer a host of benefits for businesses that use them in their day-to-day operations. Some of these are:
1. Enhanced productivity: Robot Arm Claws can perform tasks 24/7 without any breaks or downtime. They work at a faster pace than humans, making them ideal for mass production environments.
2. Increased precision: Robot Arm Claws can perform very precise tasks with an accuracy rate of up to 0.5mm. This level of precision makes them perfect for tasks that require extreme accuracy, such as high-tech assembly and testing.
3. Improved safety: Robot Arm Claws eliminate the need for humans to perform dangerous tasks, reducing the risk of accidents in the workplace. This improves safety, reduces downtime, and lowers the liability exposure of the business.
4. Reduced labor costs: Once programmed, Robot Arm Claws operate autonomously, reducing dependence on human labor and lowering overall labor costs.
Applications of Robot Arm Claws
Robot Arm Claws are versatile machines that can be used in a wide range of industries, including manufacturing, food processing, packaging, chemical processing, and more. Some of the applications of Robot Arm Claws are:
1. Pick-and-Place: Robot Arm Claws can be used to pick up objects at one location and place them at another. This makes them ideal for tasks such as sorting, palletizing, and packaging.
2. Assembly: Robot Arm Claws can be used to assemble products with precision, making them ideal for industries that require high accuracy assembling.
3. Inspection and testing: Robot Arm Claws can be used with cameras and sensors to inspect products and test them for quality control.
The Future of Robot Arm Claws
The future of Robot Arm Claws looks bright as industries continue to embrace industrial automation. The technology behind Robot Arm Claws is evolving, and new features are being added to make them even more efficient and versatile.
In conclusion, Robot Arm Claws are transforming the industrial landscape, reducing costs, and enhancing productivity. They are ideal for businesses that require high precision, speed, and safety in their operations. As industries embrace automation, Robot Arm Claws are poised to play an even more significant role in the future of manufacturing and other industrial applications.
Company News & Blog
4-Axis Stepper Motor Driver Card for MACH3 LPT Port Now Available on NVCNC.NET
If you are looking for a reliable and efficient way to control your 4-axis stepper motor, look no further than the MACH3 LPT Port 4 Axis Stepper Motor Driver Card. This versatile and powerful device from Novusun CNC controller is perfect for a wide range of applications, including CNC machining, woodworking, and robotics.At its core, the MACH3 LPT Port 4 Axis Stepper Motor Driver Card is designed to provide precise and accurate control over your stepper motor system. With its advanced microstepping technology, this card can deliver smooth and seamless motion control for even the most intricate and demanding tasks.One of the key benefits of this stepper motor driver card is its compatibility with a wide range of CNC controllers and software platforms. Whether you are using a Novusun CNC controller, a Nvum CNC controller, or any other popular CNC software program, the MACH3 LPT Port 4 Axis Stepper Motor Driver Card can seamlessly integrate with your existing setup and provide reliable, consistent performance.Perhaps one of the most impressive features of this stepper motor driver card is its ability to handle multiple motor axes simultaneously. With support for up to 4 axes of control, this card can handle even the most complex and demanding machining tasks with ease.Of course, no stepper motor driver card would be complete without a robust and user-friendly control interface. The MACH3 LPT Port 4 Axis Stepper Motor Driver Card includes an intuitive and easy-to-use interface that allows you to fine-tune your motor control settings and monitor your system's performance in real-time.To sum it up, the MACH3 LPT Port 4 Axis Stepper Motor Driver Card from Novusun CNC controller is a versatile and reliable solution for controlling your stepper motor system. With advanced microstepping technology, multi-axis support, and a user-friendly interface, this card is a must-have for any serious CNC hobbyist or professional.
Affordable CNC Retrofit: How to Upgrade Your Machine Without Buying a New One
In the world of manufacturing, CNC machines play a key role in the production process. These machines utilize computer numerical control (CNC) technology to automate the manufacturing process, resulting in increased efficiency and accuracy. However, like any other piece of machinery, CNC machines can become outdated over time, leading to decreased productivity and an increased risk of downtime. This is where CNC retrofit comes into play.What is CNC Retrofit?CNC retrofit is the process of upgrading an older CNC machine by replacing outdated CNC components with new, state-of-the-art technology. This involves a complete overhaul of the machine's electrical and mechanical systems, including the CNC controller, servo drives, motors, and other key components. The result is a machine that functions like new, but at a fraction of the cost of buying a new machine.Why Choose CNC Retrofit over Buying a New Machine?There are several reasons why CNC retrofit is a better option than buying a new machine. Firstly, retrofitting a machine is much cheaper than buying a new one. Retrofitting involves upgrading existing components rather than buying an entirely new machine, which can save businesses substantial amounts of money. Additionally, retrofitting can be completed much faster than buying a new machine, which can take months to be delivered and installed.Another advantage of retrofitting is that it allows businesses to keep the machines they are familiar with. Many companies have invested heavily in their CNC machines, and retrofitting allows them to continue using these machines rather than having to learn how to use new equipment. This also means that there is no steep learning curve or downtime associated with retrofitting, as employees are already familiar with the machines.CNC retrofitting also offers increased flexibility in terms of machine capacity and functionality. Upgrading to newer technology can result in more precise control over the machine and improvements in speed and accuracy. It can also provide additional features such as new software, increased memory, and expanded storage capabilities.Is CNC Retrofit Right for Your Business?CNC retrofitting is an excellent option for businesses looking to extend the lifespan of their CNC machines without having to purchase new ones. It is a cost-effective and efficient way to upgrade outdated equipment, allowing companies to keep up with technological advancements while staying within their budget.Ultimately, the decision to retrofit depends on the unique needs and circumstances of each business. Factors such as the age and condition of the machine, the cost of new equipment, and the business's financial situation should all be considered when deciding whether to retrofit a CNC machine.If your business is considering CNC retrofitting, YARA-AUTOMATION can help. Our team of experienced engineers can evaluate your current CNC system and design a retrofit solution that meets your specific needs. We use the latest technology to ensure that your machine is operating at peak performance, and our retrofit solutions are tailored to your budget and timeline.ConclusionCNC retrofitting is a cost-effective and efficient way to upgrade outdated CNC machines. It offers a range of benefits, including increased functionality, improved accuracy, and decreased downtime. If your business is considering CNC retrofitting, YARA-AUTOMATION can help. Contact us today to learn more about our retrofit solutions and how we can help your business stay competitive in today's fast-paced manufacturing environment.
Get Laser Welding Robots for Your Business - Discover the Compatible Models
Robotics and automation have become an integral part of the modern manufacturing industry, and they continue to shape production processes across almost all industrial sectors. Since their invention, robots have grown more sophisticated, with the incorporation of the latest technological advancements, including laser welding. As a result, they have become more efficient and dependable, delivering better outputs within shorter periods.RobotWorx, a proficient and dependable provider of high-quality industrial robotic solutions, has launched a gamut of new and reconditioned robots that cater to the laser welding application. The newly added robots include those that are compatible with laser welding technology to deliver precise outputs for maximum efficiency. RobotWorx has established a reputation for excellence and dependability, offering top-of-the-line products to its clients across the globe. Every RobotWorx product is manufactured under strict quality checks, ensuring optimal functionality and durability.Laser welding is an advanced welding technique that uses a high-powered laser beam to join materials. It is commonly used in areas where accuracy, speed, and minimal distortion are essential. The laser beam concentrates the energy on a small surface area, resulting in a more rapid heating and cooling process within the joint, minimizing the amount of heat deposited into the surrounding material. This improves the material's potential to resist wear and tear, damage, and cracking. The result is a joint that is precise, dependable, and efficient, making it popular across various industrial applications.ABB laser welding robots from RobotWorx offer a reliable, efficient, and cost-effective solution for businesses looking to improve their productivity and efficiency, reducing production processes' downtime. These robots have a high payload capacity, providing an excellent option for large-scale production operations. ABB robots offer precision, speed, and a high level of accuracy, making them a preferred choice for laser welding operations. RobotWorx offers both new and reconditioned ABB robots, catering to the diverse needs of clients across various industries.The use of laser welding robots from RobotWorx offers a range of benefits that make them an ideal option for many businesses. Their improved productivity and speed make them an attractive option for industries looking to enhance their cost-effectiveness. Additionally, they allow for more accuracy and consistency in parts manufacturing and the reduction of human error, leading to less waste and higher-quality precision products.RobotWorx offers a comprehensive range of new and reconditioned robots that cater to a diverse range of applications. With a wide selection of industrial robots available, clients can choose the right robots that suit their specific needs, provide optimal performance and durability, and are budget-friendly. With the inclusion, removal or modification of skills, these robots can perform many tasks, including material handling, welding, and painting, streamlining the production process and enhancing process efficiency.In conclusion, the introduction of ABB laser welding robots from RobotWorx offers a game-changing solution to automate the welding process in an industrial setting. The use of these robots provides unmatched precision, speed, higher efficiency, and cost-effectiveness in the production process, making manufacturing a streamlined process that delivers quality products at an affordable price. RobotWorx continues to provide top-of-the-line robotic solutions to businesses worldwide, helping them stay competitive and maintain their position as industry leaders.
Expert Q&A on Robotic Arms for Engineers, Researchers, Hobbyists, and Students
Industrial robotic arms have increasingly transformed the manufacturing and industrial sectors over the years. They are automated devices designed to move objects, parts, and tools in a repetitive and precise manner. They offer high-speed operations, accuracy, precision, and safety, which consequently translates to a boost in productivity and efficiency.Industrial robotic arms are designed to perform several functions such as welding, painting, material handling, and assembly line operations, among others. They are also equipped with control software that can be programmed to perform specific tasks. This feature allows them to handle complex and delicate operations that are difficult for humans to execute.The rise of industrial robotic arms has also led to the development of artificial intelligence-enabled robots capable of performing more complex tasks. These robots come with embedded sensors that enable them to sense and react to their environment. Such robotic arms are vital in hazardous environments such as nuclear plants where human presence would be dangerous.One major advantage of the industrial robotic arm is precision. Unlike humans, machines can repeat the same action with high accuracy and precision. Therefore, companies that rely on the precision of manufacturing processes such as pharmaceuticals, electronics, and aerospace can now produce high-quality products with reduced waste.Moreover, industrial robotic arms provide a safer working environment for employees. They are designed to work in hazardous environments such as high-temperature and toxic areas and can withstand vibrations and other harsh conditions. This feature allows workers to operate in a safer work environment without exposure to hazardous substances and dangerous equipment.Another benefit of using industrial robotic arms is that they reduce production costs. Automated robots can increase productivity and efficiency, which can lead to significant cost savings. They can work 24/7, which ensures that production processes run continually, reducing downtime and increasing throughput.Furthermore, the use of industrial robotic arms enables flexible production capabilities. They can be programmed to work on different tasks and adapt to new products' specifications quickly. This flexibility helps manufacturers adjust to market demand changes seamlessly.In conclusion, the industrial robotic arm has significantly transformed the manufacturing and industrial sectors owing to its accuracy, precision, safety, and efficiency. Its use will undoubtedly continue to grow, resulting in increased productivity, reduced costs, and a safer working environment for employees.
Aircraft Turbo System Pressure Controllers Available for Purchase at QAA - Get New, Used, or Overhauled Parts Today!
An innovative new aircraft component has been developed, offering improved performance for aircraft turbo systems. The Absolute Aircraft Turbo System Pressure Controller is a state-of-the-art device that promises to enhance the safety and reliability of air travel.With a track record of producing high-quality parts for the aviation industry, the supplier QAA has announced that it is offering the Absolute Aircraft Turbo System Pressure Controller for sale. This cutting-edge component promises to take aircraft systems to new heights by enabling precise control and regulation of turbocharger speed.The Absolute Aircraft Turbo System Pressure Controller has been meticulously engineered by a team of experts with extensive experience in the aviation industry. It incorporates the latest technological advances to deliver unparalleled performance. The device has been rigorously tested to ensure that it meets the highest standards of safety and effectiveness.Turbo systems play a critical role in the operation of aircraft. They are responsible for providing the necessary power to propel planes through the air. The Absolute Aircraft Turbo System Pressure Controller optimizes this process, maximizing the efficiency and effectiveness of turbo systems to deliver unparalleled performance.Integrating the Absolute Aircraft Turbo System Pressure Controller into aircraft systems will enable pilots to more effectively control the speed of turbochargers. This will help optimize engine efficiency, which in turn can lead to significant fuel savings. This is important not only from an operational perspective but also in terms of environmental sustainability.The Absolute Aircraft Turbo System Pressure Controller's design is straightforward, making it easy to install and integrate into existing turbo systems. It is highly adaptable, suitable for use in a variety of aircraft types and sizes. It is available in new, used, and overhauled versions, ensuring that all aircraft owners and operators can access this critical component.The supply of this innovative device by QAA demonstrates the company's commitment to offering high-quality, reliable components to the aviation industry. They have earned an excellent reputation for their ability to provide exceptional customer service and knowledgeable support to their clients.As the aviation industry continues to evolve and grow, innovation in component development remains crucial. Products like the Absolute Aircraft Turbo System Pressure Controller represent the next generation of technology designed to improve aircraft performance, safety, and efficiency.As air travel continues to become an increasingly important aspect of modern life, the Absolute Aircraft Turbo System Pressure Controller represents a significant step in advancing the capabilities of aircraft systems. The product's precision controls and advanced technology promise to revolutionize the way that turbo systems operate, offering potential benefits in terms of fuel savings, environmental sustainability, and safety.In conclusion, the Absolute Aircraft Turbo System Pressure Controller is a revolutionary product that offers a range of benefits to the aviation industry. The device provides precise control over turbo system speed, maximizing efficiency and performance. Its innovative design is easy to install and highly adaptable to a variety of aircraft types. The Absolute Aircraft Turbo System Pressure Controller represents the next iteration of aviation technology, with the potential to improve the safety, reliability, and sustainability of air travel.
CNC Software for Stepper Motors and Drivers: Powerful Tools for Precision Manufacturing
The world of CNC machines is constantly evolving as technology advances. Among the many components that make up a CNC machine, the CNC motor is one of the most important. In this article, we will delve deeper into what CNC motors are and why they are crucial to the functioning of CNC machines.What is a CNC Motor?A CNC motor is an electronic device used to drive the movement of a CNC machine's spindle or axis. These motors can be grouped into two primary types: stepper motors and servo motors.Stepper motors are the most commonly used type of CNC motor. They are known for their ability to move the axis in precise, predetermined increments, making them highly accurate. Stepper motors are also relatively easy to control, making them an excellent choice for beginners.On the other hand, servo motors are used in more advanced CNC machines. They are more complex than stepper motors, and they offer higher power and speed. Servo motors are commonly used in industries that require high-precision machining, such as aerospace and defense.Why are CNC Motors So Important?CNC motors are crucial to the functioning of CNC machines. They play a significant role in ensuring that the machine operates precisely and predictably. A well-tuned CNC motor is essential to the end product's quality.In addition to precision and accuracy, CNC motors significantly impact the CNC machine's overall performance. The motor's speed, torque, and acceleration parameters can influence the machine's capabilities. For instance, a high-speed motor may be capable of producing high-quality results in less time, while a motor with a higher torque may be able to cut through tougher materials.Choosing the Right CNC MotorThere are several factors to consider when choosing the right CNC motor for your machine. These include:1. Torque: The torque of a motor is the amount of force it can apply to a system. Higher torque means greater strength, making it easier to cut through tough materials.2. Speed: The speed of a motor is measured in revolutions per minute (RPM). Faster motors can produce quicker cuts, but precision may suffer.3. Stepper vs. Servo: As mentioned earlier, stepper motors are more accurate but slower, while servo motors are faster but less accurate.4. Power: More power means that the machine can handle more difficult tasks, but it may also lead to increased operating costs.5. Control: Determine how much control you want over the motor's settings. Some motors come with software that allows you to fine-tune specific parameters, while others may require manual adjustments.In conclusion, CNC motors play an integral role in the functioning of CNC machines. Their precision, power, and speed parameters significantly impact the quality of the end product. When choosing the right motor for your CNC machine, consider the torque, speed, stepper vs. servo, power, and control. With the right motor, you can take your CNC machining to the next level.
Discover the Latest Innovations in Robotic Arm Technology
Robotic Arm Suppliers: The Future of ManufacturingRobotic arms have dramatically changed the way manufacturing processes are conducted. Today, robotic arm suppliers give manufacturers global access to automation, providing higher production efficiency and product consistency. Robotic arms are versatile, suitable for a wide range of industries, from automotive to electronic assembly. Introducing automation into your facility through robotic arm suppliers is the way to go if you want to take your manufacturing process to the next level.Robotic arms work by automating repetitive tasks, taking the place of manual labor to increase productivity. They are also cost-effective as they have the ability to replace multiple workers, requiring only routine maintenance. With the high levels of versatility and precision provided, robotic arms are now being used in a wider range of industries than ever before.Automotive manufacturing is one of the industries that have primarily relied on robotic arms. Car manufacturers use robotic arms to perform several different tasks, including spot welding, handling and transferring parts, and assembling components. Robotic arms can work in challenging and hazardous conditions like fumes, heat, and sharp parts, providing safety for human workers.Another industry that has seen a lot of benefits from robotic arm suppliers is the electronics industry. In this field, robotic arms have become essential due to their precision, high speed, and accuracy in handling delicate and small parts. They are often used for circuit board assembly, testing, and packaging, dramatically reducing the need for human labor.Packaging industries also use robotic arm suppliers to automate tasks such as palletizing, case packing, and assembling. Robotic arms can detect, pick, and place different items with speed and precision, allowing for increased production capacity and consistency in packing.One of the key benefits of robotic arm suppliers is their versatility. They can be programmed to perform complex tasks and adapt to different workstations, making them ideal for small-scale and large-scale manufacturing facilities. Robotic arms can also be customized to fit specific needs such as different end-effectors for specific tasks, increasing their flexibility.In addition, robotic arm suppliers offer key advantages in the areas of safety, adaptability, and maintenance. With less manual labor needed, the risk for workplace accidents is greatly reduced. They are easy to program, learn quickly, and have the ability to adjust to different work demands.Finally, maintenance is relatively low compared to traditional manufacturing processes. Robotic arms require only routine maintenance such as oil changes and cleaning, resulting in less downtime and lower maintenance costs.ConclusionRobotic arm suppliers have changed the way manufacturing processes operate today. They have dramatically increased production efficiency, facilitated product consistency, and significantly reduced the need for manual labor in the manufacturing process. The benefits of introducing robotic arms into any manufacturing facility are immense. With increased deployment in different industries, it's certain that robotic arms will continue being a part of the future of manufacturing. Contact your nearest robotic arm supplier today and embrace the future of manufacturing.
CNC Controls Engineer Job Opportunities in Various Locations - Apply Now!
CNC Controls Engineer Job at Multiple Locations – Apply Today!Attention Engineers! Siemens is currently seeking talented CNC Controls Engineers in multiple locations. At Siemens, we are committed to using digital technologies to drive progress and improve people’s lives. As a CNC Controls Engineer, you will be at the forefront of this digital revolution. You will have an opportunity to work with cutting-edge technologies in a dynamic work environment.What is a CNC Controls Engineer?As a CNC Controls Engineer, you will be responsible for programming, commissioning, and troubleshooting computer numerical controllers (CNC) used in manufacturing. These controllers are essential in modern CNC machines which can perform precision cuts, drilling, and milling operations with the help of computer programs. Industries such as aerospace, automotive, medical devices, and oil and gas rely on CNC machines to manufacture high-quality products efficiently and cost-effectively.Why Work at Siemens as a CNC Controls Engineer?Siemens is a world leader in industrial automation. Our CNC Controllers are designed to offer precision, efficiency, and productivity to our customers. As a CNC Controls Engineer, you will have access to Siemens’ expertise and technology. You will work with state-of-the-art equipment and be given the tools to succeed. Siemens is committed to providing its employees with excellent benefits, continuous professional development, and a supportive work environment.Skills and Qualifications Required for CNC Controls Engineer PositionTo qualify for this position, candidates must have the following:1. A Bachelor's Degree in Electrical, Mechanical, or Computer Engineering2. Experience in programming and commissioning of CNC machines3. Familiarity with Siemens CNC Controllers, including Sinumerik and Fanuc4. Excellent communication skills, attention to detail, and problem-solving abilitiesRoles and Responsibilities of CNC Controls Engineer• Develop and maintain CNC control programs• Identify, troubleshoot, and resolve technical problems• Collaborate with other departments to ensure smooth production processes• Perform continuous improvement activities to enhance machine performance and increase efficiency• Stay current with technological advancements and communicate new ideas to improve productionFinal ThoughtsIf you have a passion for cutting-edge technologies and manufacturing, and if you love working in a dynamic team environment, then this opportunity is for you. By joining Siemens as a CNC Controls Engineer, you will have access to Siemens’ expertise and technology, as well as develop new skills. So, don't wait any longer, apply today, and become part of the Siemens team!
5 Axis CNC Interface Adapter Breakout Board - Ideal for Mach3 and Other Software Control. USB Power Supply for Secure Performance. Anti-Reverse Function and Wide Voltage Input Range. Isolated Input Signals for Reliable Performance.
In the world of CNC machining, having a reliable and efficient interface adapter is crucial to ensure smooth operation and precise results. The 5 Axis CNC Interface Adapter Breakout Board Stepper Motor Driver Mach3 by mhenga is a top-of-the-line product that offers great versatility and compatibility.One of the main benefits of this adapter is its full support for MACH3 and other computer software that support parallel port control. This makes it easy to integrate with existing systems and ensures seamless communication between all components.Another great feature of this adapter is its USB power supply and peripherals powered phase separation. This not only provides greater convenience but also protects computer security by separating high voltage operations from the computer.In terms of voltage input, the mhenga adapter offers a wide range of options with support for 12-24V. It also has an anti-reverse function that provides added safety and protection against electrical shorts or mishaps.When it comes to input signals, the adapter offers the capability to isolate all the light lotus inputs. This means that all signals are isolated for added safety and protection against interference. Moreover, the brand name can be removed for greater customization and branding opportunities.Overall, the 5 Axis Cnc Breakout Board offered by mhenga is a highly versatile product that offers excellent compatibility and functionality. It is a must-have for anyone looking to improve their CNC machining capabilities and achieve better results.
Latest Developments in Robotic Arm Technology: News and Updates
The Future of Robotic Arms: Advancements in Technology and UsageRobotic arms have come a long way since their inception in the 1950s. Once used only for industrial purposes, they are now being utilized in various fields such as healthcare, agriculture, and space exploration. The advancement of technology has paved the way for new possibilities and improved capabilities of robotic arms.Brand name is one of the leading companies in robotic arm technology. Their robotic arms are designed to handle precise tasks in various industries, from manufacturing to medical procedures. The technology behind these arms has been improved over the years, making them more accurate, efficient, and versatile.One of the most notable advancements in robotic arm technology is the development of AI algorithms. These algorithms allow the arms to learn and adapt to their environment, making them more autonomous and less reliant on human intervention. This has led to improved precision in manufacturing processes as well as safer and more effective medical procedures.In healthcare, robotic arms have become an essential tool for surgeries. They offer greater precision and control, allowing surgeons to perform complex procedures with ease. Robotic arms can also take on the role of an assistant, holding instruments, retracting tissue, and providing a clear view of the surgical site, enabling the surgeon to operate with greater ease and efficiency.Robotic arms are also being used in the agriculture industry, particularly in harvesting crops. These arms are equipped with sensors that can detect when a fruit or vegetable is ripe, allowing for a more efficient and timely harvest. Additionally, robotic arms can perform repetitive tasks, such as picking fruits or sorting produce, which reduces the need for manual labor and improves productivity.In space exploration, robotic arms are being used to perform maintenance and repair tasks on satellites and spacecraft. Robotic arms can perform tasks in space that are difficult or dangerous for humans to do. These arms can be controlled remotely from Earth and can be used to inspect, repair, or even assemble parts in space.Brand name is also developing technology that allows for multiple robotic arms to work together in synchrony to perform complex tasks. This technology is particularly useful in manufacturing, where multiple arms can work together to assemble products, increasing efficiency and reducing production time.The future of robotic arms looks promising. With advancements in technology and increased usage in various industries, there are endless possibilities for these machines. Robotic arms will continue to be developed and improved upon, making them more efficient, precise, and versatile than ever before.As the demand for robotic arm technology grows, companies such as brand name will continue to play a critical role in the development and implementation of these machines. With their expertise and innovation, they will pave the way for a future where robotic arms are an integral part of our lives.