New Method for Controlling Jointed Arm Robots Using Integrated Computer Vision System
By:Admin
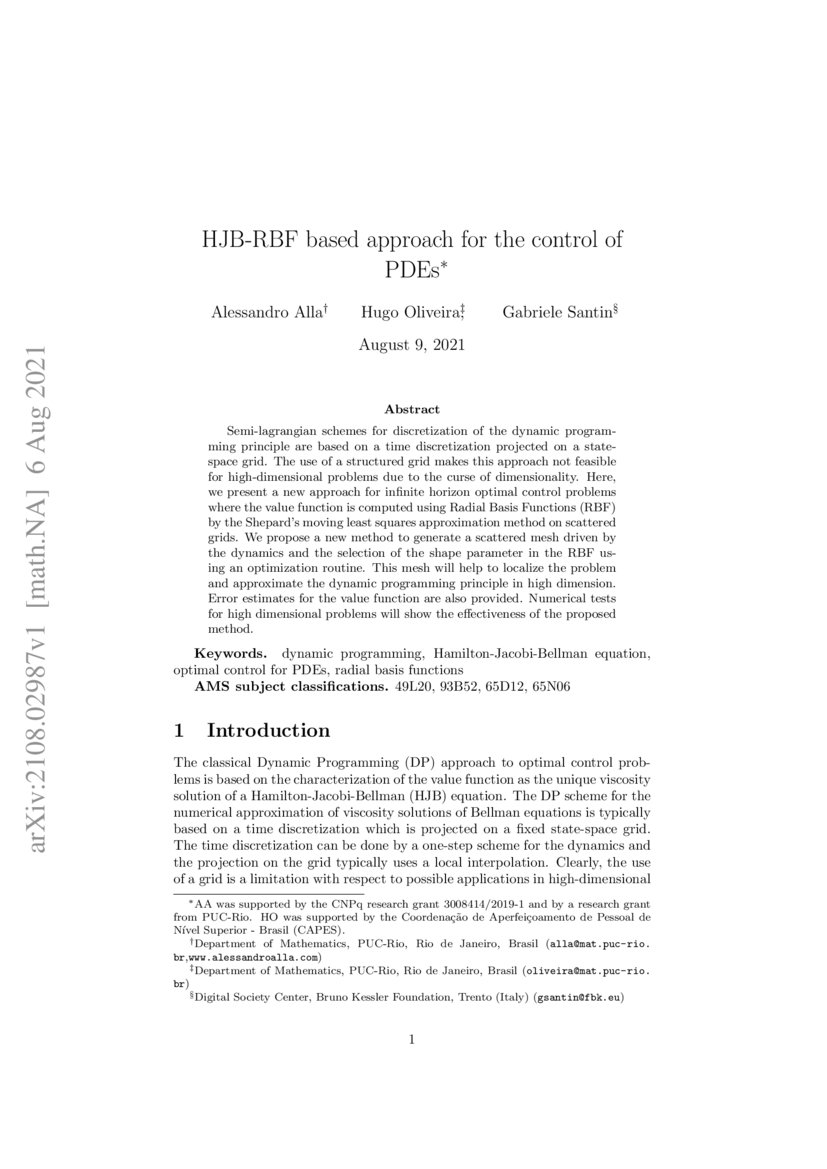
In today's manufacturing industry, automation plays a crucial role in improving efficiency and reducing costs. Robots are increasingly being used for repetitive or dangerous tasks, and their performance depends on sophisticated control systems. One of the key challenges in controlling robots is to accurately track the position and movement of objects in the workspace. This is where computer vision technology can make a significant difference.
Computer vision is an interdisciplinary field that combines computer science, optics, and artificial intelligence to develop systems that can interpret and understand images or videos. Computer vision can be used to develop self-sustained autonomous systems that can work without human intervention. In this context, computer vision can be used to control jointed arm robots based on the position of the moving object using an integrated computer vision system.
The jointed arm robot is a type of robot that consists of multiple linked segments that can move in multiple axes. The jointed arm robot can perform complex tasks that require a high degree of accuracy and precision. Examples of applications of jointed arm robots include welding, painting, assembly, and material handling.
The approach proposed in this paper uses a simple web camera placed above the work cell to capture the continuous images of a conveyor and a jointed arm robot that connected to a microcontroller through the computer. The position of an object tracked, and its features are extracted from the captured image frame by subtracting its background using the Gaussian Mixture Model (GMM). The output images of GMM further processed by image processing techniques to extract the shape, color, center coordinates.
The extracted coordinates of the objects of interest used as input for the controller to activate the base rotation of a joint arm robot to perform different manipulations. The algorithm evaluated on an indigenously fabricated work cell integrated with a computer vision setup. The results show that the proposed approach is effective in controlling the jointed arm robot based on the position of the moving object.
Computer vision technology has several advantages that make it ideal for controlling robots. First, it can work in real-time, which is essential for controlling robots that need to operate in dynamic environments. Second, it can deal with complex and noisy data, such as images or videos, and extract relevant information. Third, it can learn and adapt to changing conditions, which is crucial for autonomous systems that must operate under different conditions.
In conclusion, the use of computer vision technology to control jointed arm robots based on the position of the moving object is a promising approach that can improve efficiency and reduce costs in the manufacturing industry. The proposed approach provides a simple and effective way to track the position of objects in the workspace and control the jointed arm robot accordingly. The use of computer vision technology in the manufacturing industry is likely to increase in the future as the technology matures and becomes more accessible.
Company News & Blog
Expert Answers for 3D Printing Enthusiasts – 3D Printing Stack Exchange Q&A
*Note: Due to the lack of information and context provided, the following blog is a general overview of CNC controllers and does not directly refer to any specific brand or model.*Title: Demystifying CNC Controllers: Optimizing Precision for 3D PrintingIntroduction:In the realm of 3D printing, nothing determines the quality and precision of your prints quite like the performance of your CNC controller. A CNC (Computer Numerical Control) controller acts as the brain behind the operation, responsible for translating digital designs into physical objects. In this blog, we will explore the fundamentals and functionalities of CNC controllers, equipping you with the knowledge to optimize your 3D printing experience. So, let's delve into the world of CNC controllers and unlock the full potential of your 3D printer!Understanding CNC Controllers:A CNC controller is essentially a device or software that comprises the electrical and mechanical components necessary to control the movement of a CNC machine. In the case of 3D printing, it dictates the precise motion of the 3D printer's print head to create intricate layer-by-layer designs. By leveraging various algorithms and firmware, CNC controllers ensure that the printer follows the desired path and accurately extrudes the filament required to build the model.Types of CNC Controllers:There are primarily two types of CNC controllers commonly used in 3D printing: standalone controllers and PC-based controllers. Standalone controllers are independent units, often embedded within the 3D printer itself. They offer a user-friendly interface and are typically equipped with an LCD display, buttons, and a rotary encoder. On the other hand, PC-based controllers rely on software running on a computer, which communicates with the 3D printer through a USB connection or an Ethernet interface.Key Features and Functionalities:1. Motion Control: The CNC controller precisely controls the movement of the printer's axes, namely X, Y, and Z, to ensure accurate positioning of the print head. This aspect is crucial for achieving intricate details and preventing any deviations or inaccuracies during the printing process.2. Extruder Control: Another critical functionality of a CNC controller is managing the extruder, which controls the flow and temperature of the filament during the printing process. It ensures smooth extrusion, proper filament retraction, and consistent layer adhesion, resulting in clean and cohesive prints.3. Endstops: CNC controllers often incorporate endstop functionality, which utilizes mechanical or optical sensors to determine the limits of the printer's movement. These sensors help prevent any collisions or unauthorized movement beyond the designated print area, protecting both the printer and the model being printed.4. File Compatibility: The ability to interpret and execute specific file formats is a crucial feature of CNC controllers. Most 3D printers rely on G-code, a programming language that describes the movements, speeds, and extrusion settings required to create a print. A capable CNC controller should be compatible with the commonly used G-code formats to ensure seamless compatibility with various design software.Maximizing Precision with CNC Controllers:To optimize the precision and quality of your 3D prints, consider the following factors when selecting or fine-tuning your CNC controller:1. Stepper Motor Resolution: The resolution of the stepper motor used in the CNC controller affects the accuracy of the printer's movements. Opt for higher-resolution stepper motors to ensure smoother and more precise motion control.2. Calibration: Calibrating your CNC controller and printer is essential. Properly tuning the steps per millimeter for each axis and fine-tuning the extruder's steps per millimeter ensures accurate positioning and consistent filament extrusion, reducing the chances of print defects or imperfections.3. Firmware Upgrades: Stay up-to-date with the latest firmware releases for your CNC controller. Manufacturers often release firmware updates to improve performance, add features, or address any reported issues. Regularly updating your firmware can significantly enhance the printing experience.Conclusion:A CNC controller plays a pivotal role in determining the precision and overall quality of your 3D prints. By understanding the functionalities and fine-tuning various settings, you can harness the full potential of your 3D printer. Whether you opt for a standalone or PC-based CNC controller, remember to prioritize features like motion control, extruder management, and file compatibility to ensure optimal performance. Invest time in calibrating and upgrading your CNC controller to unlock the highest levels of precision and efficiency in your 3D printing projects.
10-60V 20A Soft Start PWM DC Motor Speed Controller with Blocking Protection
– Soft Start – PWM – 20A Current LimitWhen working with DC motors, controlling the speed is a crucial step in ensuring that the motor operates efficiently. One of the most effective ways to control the speed of a DC motor is through a DC motor speed controller. In this blog post, we will be discussing the features and benefits of the 10-60V 12V 24V 36V 20A PWM DC Motor Speed Controller Soft Start Switch TE1255.Soft Start FeatureOne of the standout features of this DC motor speed controller is the soft start feature. Soft start refers to the gradual increase in voltage that is supplied to the motor when it is turned on. This helps to avoid any damage that could be caused by the instantaneous high current that is often associated with starting up a motor. With the soft start feature, the motor is gently and gradually brought up to its operating speed, ensuring that it is protected from any sudden power surges.Blocking ProtectionAnother benefit of the TE1255 DC motor speed controller is the blocking protection feature. This feature limits the high current produced by the blocking of the motor, effectively protecting the motor from any potential damage. The blocking protection feature makes it safe and easy for you to regulate the speed of your motor.Pannel Switch ControlThe TE1255 DC motor speed controller has a panel switch control feature, which makes it much easier to control the speed of the motor. This feature ensures that you have complete control over the motor at all times, allowing you to easily adjust the speed according to your needs. With this feature, you can easily fine-tune the speed of your motor to get it exactly where you want it.Specification This DC motor speed controller supports DC brush motors that have a rated voltage of 10-60V, and has a linear output under load. It has a maximum output current of 20A, with a limited value of 20A. The TE1255 DC motor speed controller has a continuous working current of within 18A, and a maximum power of 240W. Its regulating type is regulating current, and its regulating method is a potentiometer (270 linear).In conclusion, the 10-60V 12V 24V 36V 20A PWM DC Motor Speed Controller Soft Start Switch TE1255 is an excellent choice for those looking for a reliable and efficient DC motor speed controller. With its soft start feature, blocking protection, and panel switch control, it is not only safe but also easy to use. If you want to control the speed of your DC motor, the TE1255 DC motor speed controller is a great option to consider.
New Method for Controlling Jointed Arm Robots Using Integrated Computer Vision System
, Computer Vision, Object Tracking, Image Processing, Autonomous Systems, Manufacturing Industry.In today's manufacturing industry, automation plays a crucial role in improving efficiency and reducing costs. Robots are increasingly being used for repetitive or dangerous tasks, and their performance depends on sophisticated control systems. One of the key challenges in controlling robots is to accurately track the position and movement of objects in the workspace. This is where computer vision technology can make a significant difference.Computer vision is an interdisciplinary field that combines computer science, optics, and artificial intelligence to develop systems that can interpret and understand images or videos. Computer vision can be used to develop self-sustained autonomous systems that can work without human intervention. In this context, computer vision can be used to control jointed arm robots based on the position of the moving object using an integrated computer vision system.The jointed arm robot is a type of robot that consists of multiple linked segments that can move in multiple axes. The jointed arm robot can perform complex tasks that require a high degree of accuracy and precision. Examples of applications of jointed arm robots include welding, painting, assembly, and material handling.The approach proposed in this paper uses a simple web camera placed above the work cell to capture the continuous images of a conveyor and a jointed arm robot that connected to a microcontroller through the computer. The position of an object tracked, and its features are extracted from the captured image frame by subtracting its background using the Gaussian Mixture Model (GMM). The output images of GMM further processed by image processing techniques to extract the shape, color, center coordinates.The extracted coordinates of the objects of interest used as input for the controller to activate the base rotation of a joint arm robot to perform different manipulations. The algorithm evaluated on an indigenously fabricated work cell integrated with a computer vision setup. The results show that the proposed approach is effective in controlling the jointed arm robot based on the position of the moving object.Computer vision technology has several advantages that make it ideal for controlling robots. First, it can work in real-time, which is essential for controlling robots that need to operate in dynamic environments. Second, it can deal with complex and noisy data, such as images or videos, and extract relevant information. Third, it can learn and adapt to changing conditions, which is crucial for autonomous systems that must operate under different conditions.In conclusion, the use of computer vision technology to control jointed arm robots based on the position of the moving object is a promising approach that can improve efficiency and reduce costs in the manufacturing industry. The proposed approach provides a simple and effective way to track the position of objects in the workspace and control the jointed arm robot accordingly. The use of computer vision technology in the manufacturing industry is likely to increase in the future as the technology matures and becomes more accessible.
Wholesale 6 Axis Loading and Unloading Robot for CNC Machine from China Manufacturers and Suppliers
As technology continues to evolve, manufacturing industries are looking for new and innovative ways to increase efficiency and productivity. One such innovation is the 6 Axis Loading and Unloading Robot for CNC machines. These robots are designed to assist in loading and unloading workpieces onto and off of CNC machines, effectively increasing production output and reducing labor costs.China has become a hub for manufacturing industries, and as such, it is a hotspot for the production of industrial robots. Kaberry, one of the leading 6 Axis Loading and Unloading Robot for CNC machine manufacturers and suppliers in China, offers a range of high-quality robots designed to meet the needs of manufacturing businesses.The 6 Axis Loading and Unloading Robot is a versatile and efficient machine that can be used in a variety of industrial applications. The robot has six axes of motion, allowing it to move freely and easily, and can be programmed to perform a wide range of tasks. The robot can be programmed to pick up workpieces from a conveyor belt, for example, or to place them onto a pallet for stacking. It can also be programmed to move parts from one machine to another, helping to streamline the manufacturing process.One of the key benefits of the 6 Axis Loading and Unloading Robot is its ability to work seamlessly alongside other machines in a production line. The robot can be programmed to work in a synchronized manner, ensuring that parts are loaded and unloaded exactly when they are needed. This can help to reduce downtime and improve overall efficiency, leading to increased output and profitability.Kaberry is a well-established supplier of high-quality robots, and the 6 Axis Loading and Unloading Robot is no exception. The robot is designed to be easy to use and maintain, with a user-friendly interface that allows operators to program the robot quickly and easily. The robot is also durable and reliable, ensuring that it can operate continuously without requiring frequent maintenance or repairs.In conclusion, the 6 Axis Loading and Unloading Robot is a game changer for manufacturing businesses. It offers a cost-effective solution to labor shortages and helps to increase production output while reducing downtime. If you are in the market for a reliable and efficient Loading and Unloading Robot, consider Kaberry as your supplier. With their commitment to quality and customer satisfaction, you can be assured that you are investing in a product that will help to take your business to the next level.
Servo drives support automation efficiency with the latest Profinet technology
German Automation Company Introduces Advanced Profinet Servo DriveGermany's premier automation company announced the release of an advanced Profinet servo drive that combines cutting-edge technology with reliable performance. The drive's state-of-the-art features and high level of precision make it an essential tool for anyone looking to optimize their automation process.With its powerful motor control capabilities, the new Profinet servo drive is designed to perform with excellence in demanding automation applications. The device offers high-speed processing and feedback, ensuring smooth operating functions. The advanced features within the servo drive also eliminate the need for separate add-on technology, allowing for streamlined functionality and reducing the potential for system errors. This new Profinet servo drive offers an unparalleled degree of accuracy and precision, making it the perfect fit for a wide range of automation applications. The device's cutting-edge technologies provide intelligent positioning monitoring and control while maintaining maximum uptime. This level of precision ensures that users can maintain a consistent level of output, enabling them to improve the quality of their products.One of the standout features of the new Profinet servo drive is its built-in functionality to prevent errors and downtime. The device uses advanced algorithms to analyze data feedback from the system and identify potential faults that could cause disruptions to the automation process. This proactive approach to maintenance allows users to minimize downtime and optimize productivity.The Profinet servo drive is compatible with a variety of different equipment and machinery, making it highly versatile and adaptable. Its ability to communicate seamlessly with other devices and sensors via Profinet-IO ensures high-level process integration. The device's use in industrial plants has already been proven, with successful installations in a range of industries, including automobile manufacturing, packaging, and printing.The advanced servo drive is also easy to install and use. Built-in diagnostic tools provide comprehensive feedback on the system's status, which means that operators can identify, diagnose and fix any issues quickly. This ease of use makes it an ideal solution for small to medium-sized businesses, who require the same level of precision and automation but without the need for extensive operator training.The Profinet servo drive is a game-changer for companies in need of streamlined automation solutions. Its powerful technology, advanced features, and ease of use make it the perfect fit for businesses looking to optimize their productivity and stay at the forefront of their respective industry. The new Profinet servo drive will undoubtedly change the way businesses approach their automation process, providing real-world solutions to enhance efficiency, productivity and reduce errors and downtime.In conclusion, the newly released Profinet Servo Drive by the German automation company provides cutting-edge technology combined with an easy to use interface and a wide range of applications that ensures business success and optimal productivity. This is the perfect solution for businesses looking to streamline their automation processes, optimize efficiency, reduce downtime, and increase return on investment.
How to Handle a 4WD Robot Frame as a 2-Wheel Differential Drive: Tips from Robotics Experts
Bespoke Robotics Company Launches Groundbreaking 2-Wheel Drive RobotIntroducing a powerful yet easy-to-use robot that is guaranteed to revolutionize the world of robotics as we know it. Designed and developed by bespoke robotics company need remove brand name it has been aptly named 'The Baron' and is a magnificent creation that is capable of handling rough terrains with ease.The Baron is a 4WD robot frame which is unique in its design and handling. It has 4 static wheels, all driven by a motor which provides an excellent balance of power and control. However, the company has taken a new approach towards handling it. Rather than using it as a traditional 4-wheel drive, they have designed it to function as a 2-wheel differential drive.This means that the left and right wheels of The Baron would receive the same speed and direction while making turns. This makes the robot more maneuverable while also providing it with increased traction control. It can move in any direction with ease, making it the perfect tool for various applications.The Baron robot is equipped with a state-of-the-art control system that is simple and easy to use. The system is based on an open-source platform which provides immense flexibility and customizations. The control platform is user-friendly, allowing professionals and beginners alike to operate it with ease.The robot's drive is a closed-loop system that is accurate and responsive. It has been designed with the best possible motors and sensors to provide a seamless transition from manual to autonomous mode. The robot is equipped with different sensors like IR sensors, ultrasonic sensors, etc. which ensure that it can sense its environment and make accurate decisions based on the data.Need remove brand name is a bespoke robotics company that has been designing and manufacturing robotics solutions for over a decade. They have worked with various clients worldwide to provide them with customized robotics solutions that cater to their specific needs.Based on their vast experience and expertise, the company has developed The Baron robot, which is a perfect blend of innovation, technology, and performance. They have constructed it with the highest standards, using the best materials and components, ensuring longevity and durability.The Baron is designed for various applications, ranging from education, research, surveillance, exploration, and beyond. It is versatile and can be customized to cater to different applications, providing an excellent return on investment and a software platform for data acquisition and analysis.In conclusion, need remove brand name's Baron robot is a groundbreaking innovation that will transform the way we view robotics. The company's vision and expertise have culminated in a state-of-the-art robot that is perfect for various applications. If you're looking for a powerful and easy-to-use robot, you cannot go wrong with The Baron.
Latest Advancements in Advanced 8-Axis CNC Controllers Revealed in Latest Report
In the ever-evolving technological world we live in today, precision machinery has become increasingly complex and sophisticated. In the manufacturing industry, CNC machines have become a crucial component of the production process, with their versatility and precision allowing for the manufacturing of complex and intricate components. A key element in the operation of these CNC machines is the controller, which serves as the brain that guides and regulates the movement and functions of the machine.Recently, {Company}, a leading provider of CNC machinery, has introduced a new 8-axis CNC controller that promises to revolutionize the manufacturing industry. This new controller provides a range of features and capabilities that allow for greater precision, flexibility, and ease of operation.One of the key features of this new controller is its ability to support up to 8 axes simultaneously. This means that multiple tools and functions can be operated simultaneously, allowing for greater efficiency and speed in the manufacturing process. This is particularly useful in complex and intricate components where multiple tools and functions are required to work in unison.Another key feature of this controller is its advanced control algorithm, which ensures that the machine operates with maximum precision and accuracy. This algorithm takes into account a range of factors, such as tool wear and temperature, and adjusts the machine's operations accordingly. This ensures that the machine operates at maximum efficiency and produces components of the highest quality.In addition, this new CNC controller also includes advanced software that allows for greater customization and control over the machining process. This software allows for the creation of custom tool paths, which can be tailored to specific components and manufacturing processes. This not only improves the efficiency of the process but also ensures that the components are produced to the precise specifications required.Furthermore, this new CNC controller also includes a range of safety features that ensure the machine operates safely and efficiently. This includes features such as overcurrent protection, synchronization monitoring, and emergency stop functions. These features not only protect the operators from potential hazards but also protect the machine from damage, ensuring its longevity and reliability.Overall, this new 8-axis CNC controller from {Company} promises to revolutionize the manufacturing industry by providing a range of advanced features and capabilities. Its ability to support multiple axes simultaneously, along with its advanced control algorithm and software, ensures that the machine operates at maximum efficiency and produces components of the highest quality. Additionally, its range of safety features ensures that the machine operates safely and reliably, providing peace of mind to operators and owners alike. With this new CNC controller, {Company} is once again raising the bar in precision machinery, providing solutions that assist manufacturers in meeting their production demands with ease.
Reliable Control Panels and AC Drives Supplier in Ahmedabad, India
Motor Control Panels: Ensuring Smooth and Safe Operation of your MotorsMotor control panels are a vital component in the electrical circuit of any industrial process. They play a crucial role in ensuring the smooth and safe operation of motors, and thus, their maintenance and upkeep are necessary to avoid machine shutdowns and operational delays.Motor control panels are typically used in a wide range of industrial applications, such as pumps, conveyors, compressors, fans, and other types of machinery that require precise control and monitoring of the motor's speed, torque, and direction.These control panels consist of an electrical enclosure, which houses the various control devices, such as circuit breakers, contactors, overload relays, motor starters, and other control accessories that are required to operate the motor safely and effectively.The primary function of the motor control panel is to protect the motor from damage due to overload, short circuits, overvoltage, and other hazardous conditions. This is accomplished by a combination of different types of protection devices such as thermal overload relays, electronic overloads, and other protective relays that monitor the motor's performance and intervene if necessary.Another function of the motor control panel is to maintain the quality of the electric power supplied to the motor. In industrial environments, electrical disturbances such as transient voltage surges, voltage sags, and harmonics can have a detrimental effect on the motor's performance and lifespan. The control panel includes devices such as line reactors, filters, and surge protectors that mitigate these effects and ensure dependable and efficient motor operation.Uma electro controls (Control Panel & AC Drive) in Ahmedabad, India, is a well-established manufacturer and supplier of high-quality motor control panels and other electrical solutions. Their team of experts designs and manufactures custom control panels that meet the specific requirements of the client's application. Their products are known for their durability, electrical safety, and efficiency, and they have built a reputation for being a reliable and trustworthy supplier in the industry.In conclusion, motor control panels play a critical role in ensuring the smooth and safe operation of motors in industrial processes. The selection, installation, and maintenance of these panels are crucial to preventing downtime and increasing the lifespan of the motors. A reliable and experienced supplier such as Uma electro controls (Control Panel & AC Drive) in Ahmedabad, India, can provide custom solutions that meet the client's requirements and contribute to the success of their business.